Bulldozers and motor graders are both highly versatile pieces of construction equipment. Many times they can be used interchangeably. However, they are also designed to handle different jobs better than the other. If you need to choose between the two, it’s important to know which one is most efficient for your project.
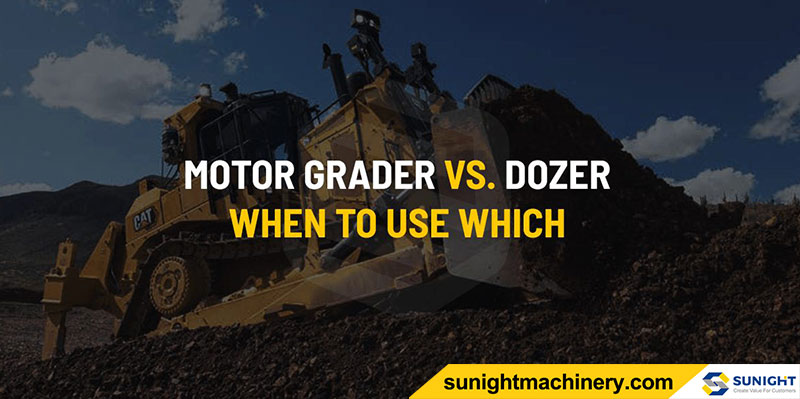
The first thing you need to consider is the demands of the job and what you need the equipment to do. You also want to know the differences between the two types of equipment as well as the disadvantages of each. In this post, we’ll compare motor graders to bulldozers to help you make the right choice.
BULLDOZER CONSTRUCTION EQUIPMENT
Bulldozers are powerful pieces of machinery capable of pushing rocks, earth, demolition debris, and other materials. They can be found in quarries, on farms, at construction sites, and a variety of other locations.
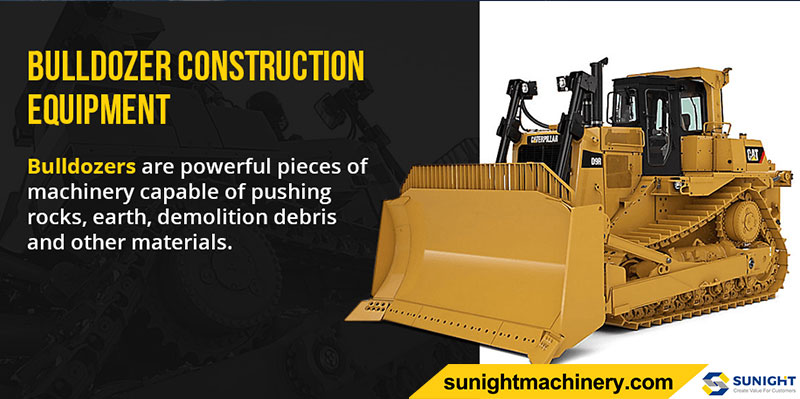
1. PARTS OF A BULLDOZER
A bulldozer consists of the tractor, which is usually a track or crawler type, mounted on metal treads. Because bulldozers often use tracks instead of wheels, they can move over rough terrain such as muddy or sandy surfaces without getting stuck. The large tracks distribute the machine’s weight evenly which also helps it move over a variety of terrains. At the front of the machine is a heavy, wide steel blade or plate used for pushing, grading, or lifting. Here’s an overview of the major components:
- Operator’s cab: The cab contains most of the controls and is enclosed by a rollover protective structure (ROPS). The wide, side-mounted tracks give operators space to step into and out of the cab.
- Track frame, track rollers, and track assembly: The track frame provides the structure for the track rollers, track assembly, and other mechanisms. The track assembly consists of a continuous chain surrounding the track frame. The chains provide a flat surface for the track rollers to move over.
- Blade: The blade is the bulldozer’s main working tool. It has a bottom cutting edge and corner bits to drift and cast material. The blade may be manually or hydraulically positioned depending on the machine. The blade can be tilted, lifted, angled, and pushed forward or backward to help complete a variety of tasks.
- Ripper: The ripper is the claw-like attachment mounted at the rear of the machine. It is raised and lowered hydraulically and used to break up or loosen various materials such as shale or asphalt. It’s also used to rip up boulders, stumps, and roots for easy removal.
- Push arms: Usually, push arms are attached to the bottom of the blade outside of the track frame.
- Pitch arms: Pitch arms are diagonal units between the blade and the push arms designed to control the blade tilt and pitch and to brace the push arms.
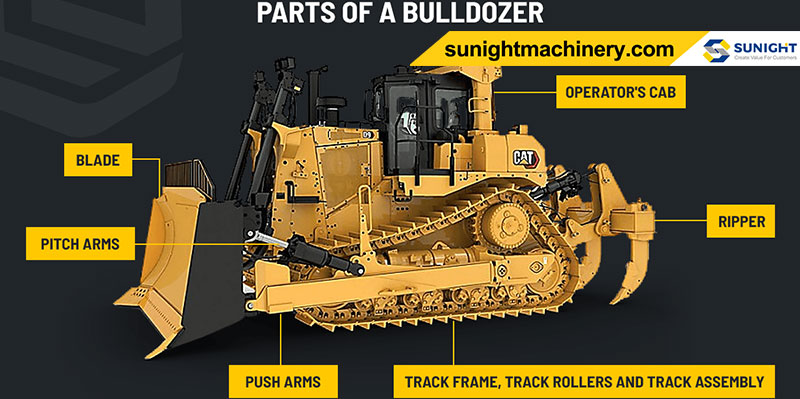
2. DIFFERENT BULLDOZER ATTACHMENTS
One of the benefits of a bulldozer is the option to use a range of attachments. This provides a lot of flexibility with one machine and prevents you from having to rent or buy other machinery. Instead, you can save time and money by renting the right attachment for the job. Some attachments you can use with a bulldozer include:
- Straight blade: A straight blade is best for drifting materials short or medium distances or to use in fine grading. This type of blade does not have any curves or side wings.
- Angle blade: An angle blade is a multipurpose tool suitable for sidecasting materials.
- U-blade: A U-blade drifts heavy loads over long distances. It has a curved shape and is taller than a straight blade.
- Box blade: A box blade is designed for grading and leveling large properties, parking lots or roadways. It may include side cutters and front and rear moldboards for maximum leveling performance.
- Winch: A winch consists of a cable or chain used to lift or haul materials, or uproot trees or stumps. It’s mounted at the rear of a dozer machine.
- It’s important to choose an attachment that will both get the job done and work with your heavy equipment. Here’s how to know if an attachment will fit your bulldozer:
- Equipment specifications: Information like your equipment’s model number, weight capacity and tipping load are all crucial criteria for selecting the right attachment.
- Attachment type: You’ll want to find out whether you will need a fabricated or a hydromechanical attachment. Because fabricated attachments work with most machines that don’t need extra hydraulics, you can use one from another manufacturer. Hydromechanical attachments, on the other hand, should come from the same manufacturer as the machine to ensure a proper fit.
- Matched configurations: To ensure proper function, the attachment you choose should match the configuration of your equipment. For instance, you should only attach a high-flow hydraulic attachment to a high-flow machine.
- Price: Of course, you’ll need to choose an attachment you can afford. Many dealerships offer the opportunity to rent equipment and attachments for operations with tighter budgets, so check with your dealer to see what options are available to you.
3. BULLDOZER USES
Despite its heavy weight, bulldozer operation is relatively easy and may be good for beginners. If a traditional track dozer doesn’t work for you or your crew, you can choose wheeled or mini dozers for higher maneuverability in smaller spaces. A smaller bulldozer may be the perfect machine for residential projects. In general, bulldozers are used to complete the following tasks:
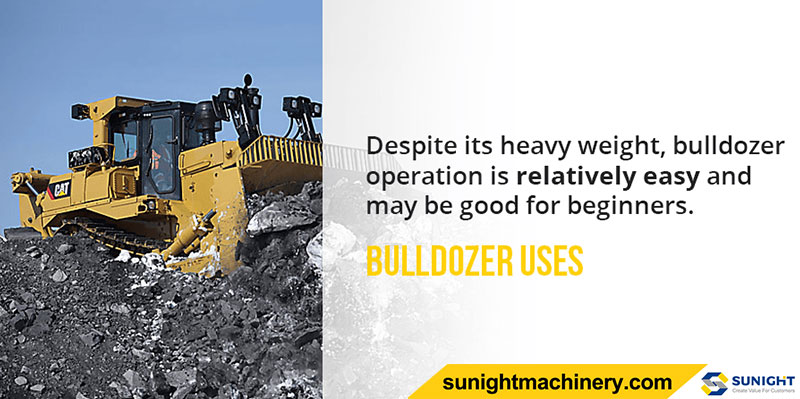
- Clearing: Bulldozers can be used to remove materials such as brush, trees, boulders, and anything else that may be embedded into the ground and in the way of a construction project. They can also remove moist topsoil to prepare for road construction. A tilted blade is a highly effective tool for removing boulders and rocks.
- Drifting: Drifting entails pushing materials straight ahead of the dozer blade. The maximum working distance depends on the blade’s capacity. For a medium-sized bulldozer, 200 to 500 feet is usually the maximum distance for drifting. Bulldozers can also be used to push debris from demolition projects.
- Spreading: Dozers are perfect for spreading fill materials such as rock or soil.
- Backfilling: Dozers can be used to backfill holes or trenches. The angle blade is the best tool for backfilling with a bulldozer.
- Finishing: Bulldozers are capable of fine grading and establishing drainage after clearing or spreading material. However, as you will see, they are not as precise as motor graders when it comes to finishing.
- Ditching: Bulldozers are useful tools for shallow digging.
- Transportation: You can transport various materials short distances with a bulldozer.
Bulldozers are commonly used in the following areas:
- Construction
- Earthmoving
- Farming
- Forestry
- Mining
- Roadbuilding
- Wrecking
A few bulldozer advantages include:
- The tracks help prevent bulldozers from sinking while traversing rough terrain.
- Using a bulldozer to remove trees is less expensive than manual felling.
- Bulldozers are strong, versatile pieces of equipment.
- Bulldozers are easier to operate than some other pieces of equipment.
- They are available in a range of sizes to suit the needs of different projects.
- They often feature comfortable cabs to improve operator safety and control.
4. DISADVANTAGES OF A BULLDOZER
Bulldozers are not designed for precision. Therefore, if you need a machine that can perform fine grading, you’ll probably want to choose a motor grader.
Another bulldozer disadvantage is they can impact the environment. They might disturb soil on sloping land and increase erosion or destroy trees. For example, one study found that bulldozers damaged 33 percent of trees on steep terrain during forest road construction.
Also, bulldozers are heavy machines. Their weight compacts soil which may lead to irrigation issues on shallow soils. Before you choose a bulldozer, consider the impact and how this can affect your project goals in the long term.
MOTOR GRADER CONSTRUCTION EQUIPMENT
A motor grader, sometimes called a grader or road grader, is a narrow multipurpose construction machine used to flatten a surface during grading projects. Generally speaking, the working principle of a motor grader machine is it uses its moldboard, or blade, for rough or fine grading. However, the moldboard’s position and pitch can be hydraulically manipulated to complete a variety of tasks.
When a project calls for fine grading, you’ll want to consider using a motor grader. Motor graders also make excellent snow removal machines. Many business owners value their motor graders above other equipment. According to a survey, almost 88 percent of the surveyed engineers and equipment operations managers called their grader their most important piece of equipment. Many industry professionals favor graders because they keep the roads in shape and are great tools for big projects.
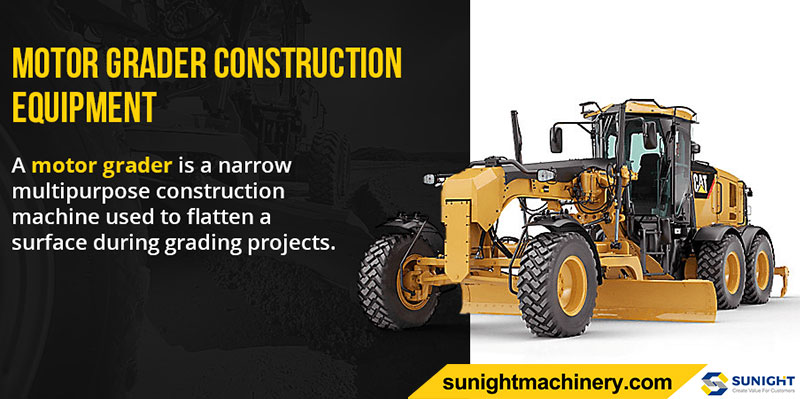
1. PARTS OF A MOTOR GRADER
A motor grader is a large piece of equipment with a unique shape. Here are some of its main components:
- Operator’s cab: In the cab, you’ll find multiple controls, levers, and a steering wheel. A windshield and large windows enclose the cab.
- Moldboard: The moldboard is a grader’s working tool. It’s usually 12 or 14 feet in length and consists of a cutting edge attached to the bottom and end bits on the sides. The moldboard is located between the front and rear axle. It can be rotated 360 degrees in either direction, allowing the operator to save time through a technique called reverse grading. It can also be shifted left or right, tilted forward or backward, and lowered and raised.
- Prime mover: The prime mover is the rubber-tired tractor-mounted at the rear. A diesel engine powers it.
- Frame: The frame is connected to the front axle and extends the full length of the grader. Its height allows enough room for the moldboard to do its job.
- Scarifier: The scarifier is located in front of or behind the front wheels and is hydraulically controlled. It uses teeth to break up compacted surfaces.
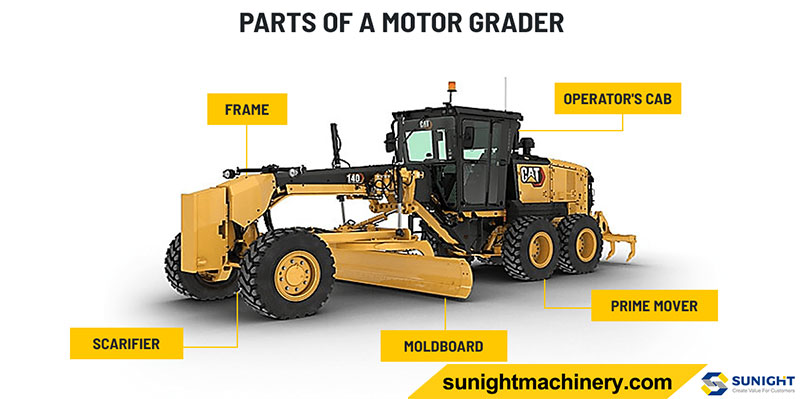
2. DIFFERENT MOTOR GRADER ATTACHMENTS
Just like a bulldozer, you can attach different blades and work tools to a motor grader such as angle blades, box blades, and U-blades. Here are other commonly used attachments:
- V-plow: A V-plow mounts to the front of the motor grader’s frame. Its high “V” shape is designed to cast material to both sides and is ideal for deep snow removal. It’s designed to dig into and lift snow.
- Tire chains: Tire chains are frequently required to improve traction in the winter. Normally used on rear-drive tires, they can also be used on front tires to reduce front end sliding.
- One-way snow plow: A one-way plow is perfect for plowing snow or ice off roads or city streets.
- Ripper: As with bulldozers, a ripper attachment is a claw-like unit used for breaking up asphalt, rocks, and other materials and is mounted at the rear of a motor grader.
3. MOTOR GRADER USES
Motor graders play an essential role in performing accurate grading and leveling. To demonstrate the importance of accuracy when it comes to roadbuilding, consider the different layers a piece of grader equipment must work with. A road consists of three layers – the surface, the base, and the subgrade. The surface may be asphalt, gravel or another material. It must provide a good surface for driving and be resistant to wear, skids and water. The base and subbase layers provide strength for the pavement surface. The base consists of compacted gravel, sand, rock, or a mix of these materials. The subgrade is the existing natural soil.
Before road construction can occur, the top 12 or 24 inches of the ground must be prepared by removing rocks, stumps, brush, and other materials. Proper drainage is also needed to keep a stable base. The right road grading equipment, like a motor grader, can accomplish all of the essential tasks in roadbuilding from start to finish, ensuring solid, long-lasting roads.
Overall, motor graders are versatile, powerful machines suitable for large projects. They may be used to complete any of the following tasks:
- Create the base for paved roads
- Set the foundation for a large building
- Create inclines
- Create drainage ditches
- Remove snow
- Mix and spread materials
- Finish grading
- Ditch cutting
- Scarifying
- High bank cutting
Motor graders are most commonly used in the following types of projects:
- Road construction
- Road maintenance and repair
- Snow removal
Some of the advantages of working with a motor grader include:
- Fast and efficient performance
- Precise capabilities cause less disturbance to the soil
- Articulated frame graders can maneuver in tight spaces
- Can drive over roads and do not need to haul between job sites
- Great for larger projects
4. DISADVANTAGES OF A MOTOR GRADER
Motor grader operation requires skill and experience. This means it may not be the best choice for employees who are new in the construction industry. Some operators say the motor grader is the most difficult machine to learn if one wants to use it to its potential. It’s true that a motor grader can do a lot of things, but it’s up to the operator to know how to use all the features.
Also, motor graders have limited traction because they use rubber tires rather than tracks. They are also not suitable for moving heavy loads like a bulldozer due to the moldboard location. Lastly, motor graders are too large for some projects.
MOTOR GRADER VS. BULLDOZER: WHICH ONE TO CHOOSE
By now you probably know which piece of equipment is best for your project. Let’s summarize the main points to help you finalize your decision. In general, bulldozers are used:
- To push large amounts of material
- For working on rough terrain
- For smaller or medium-sized projects in construction, mining, land clearing, and forestry
Motor graders are generally used for:
- Fine grading and precision
- Working in large, open areas
- Working on big projects such as roadbuilding and road maintenance